IMPACT Washington, D.C. 2019 Recap: Industry Leaders Call for Action on USMCA Trade Deal, Other Pro-Manufacturing Policies

Help Build Industry’s Future: Be a Part of IPC’s Emerging Engineer Program
Are Regional Differences in PCB Technology as Great as We Think?

IPC Day 2019 - Hungary
IPC and its partners Microsolder and ELAS, IPC licensed training centers in Hungary, welcomed more than 60 industry experts and members to IPC Day, Hungary held at the Groupama Arena, the largest football stadium in Budapest.
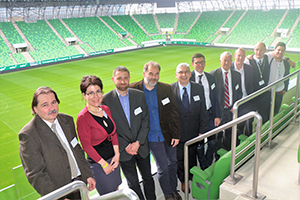
This one-day workshop provided an opportunity for attendees to network and exchange knowledge and represented an ambitious effort to expand awareness of IPC standards and activities among the dynamic electronics industry community in Hungary.
Peter Regos, Master IPC Trainer (MIT), Managing Director of Microsolder and István Hámornik, Managing Director of ELAS, gave opening remarks ahead of Philippe Léonard, IPC Europe Director, who presented information on electronics industry perspectives. Léonard walked the audience through a detailed overview of upcoming IPC activities in Europe including:
- IPC Transportation Initiative
- IPC now using DRM Protected Documents
- IPC EDGE, IPC’s online learning platform
- ICP Certified Standards Expert (CSE) certification program
- IPC-CFX, the Connected Factory Exchange for Industry 4.0
- Using J-STD-001 and IPC-A-610 together
- IPC standards and automotive addendums
- IPC standards and space addendums
- IPC standards available in Hungarian
- Industry skills gap and IPC tackling the industry’s workforce challenges
Later, Microsolder Managing Director, Csaba Császár gave a presentation on how to increase the reliability of PCBs using IPC standards.
Finally, Gábor Hámornik and Gábor Ozsváth from ELAS introduced available liquid dispensing technologies in the electronics industry that comply with IPC standards.
Attendees had the unique opportunity to learn about IPC and how to get further involved at local and European levels, network with like-minded peers and visit Hungary’s most famous football stadium.
IPC’s ambitious plan for 2019 aims to significantly increase local engagement in Europe and develop more events and education opportunities at the local level.
Interested in organising an IPC Day in your company/city? Please, contact Philippe Léonard at philippeleonard@ipc.org
Hosted by:
IPC Welcomes New Senior Director of Sales
United States Increases Tariffs on More Chinese Products
Export Controls in Flux

Engineer Connects Education, Industry and IPC
